PR Series
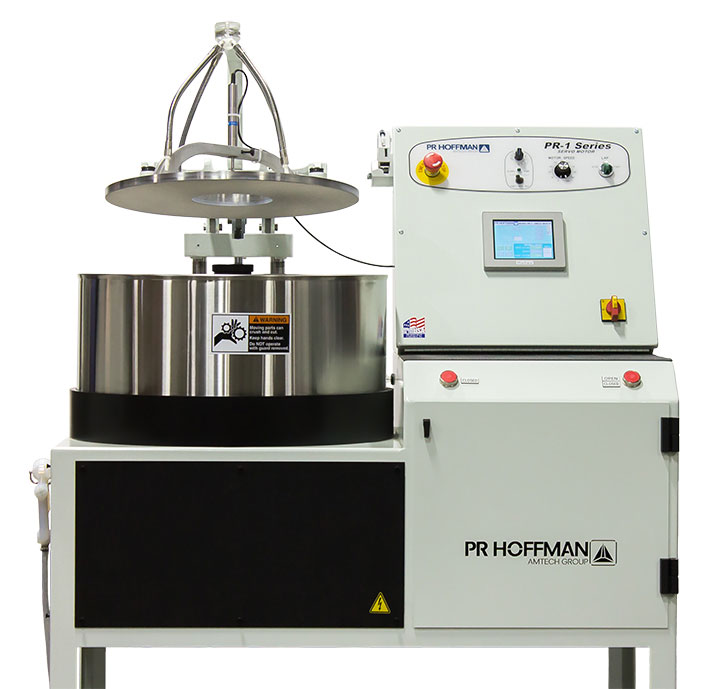
PR - 1
Equipment
- Choice of four carrier (work holder) configurations: (13) 32 tooth, (8) 50 tooth, (5) 66 tooth, or (5) 85 tooth
- Smooth cast iron plates
- Stationary bottom plate
- Floating, non-rotating top plate
- Cast iron ring and center gears
- Driven by single variable speed motor
- Mechanical transmission drives the outer ring gear and center sun gear at fixed gear ratio
- Bottom plate height adjustment mechanism
Control console
- Illuminated start/stop selector switch, master speed control knob, manual or timer control selector switch, emergency stop pushbutton and main disconnect selector switch
- Digital timer function, machine speeds, and motor loads are incorporated into touch screen operator interface
Provisions for raising and lowering the top plate
- Top plate handles and a post and hanger for storing the top plate on the 32T, 50T and 66T configurations
- Top plate lifting device operated by 2-hand safety control pushbuttons and pneumatic system on the 85T configuration
One year warranty
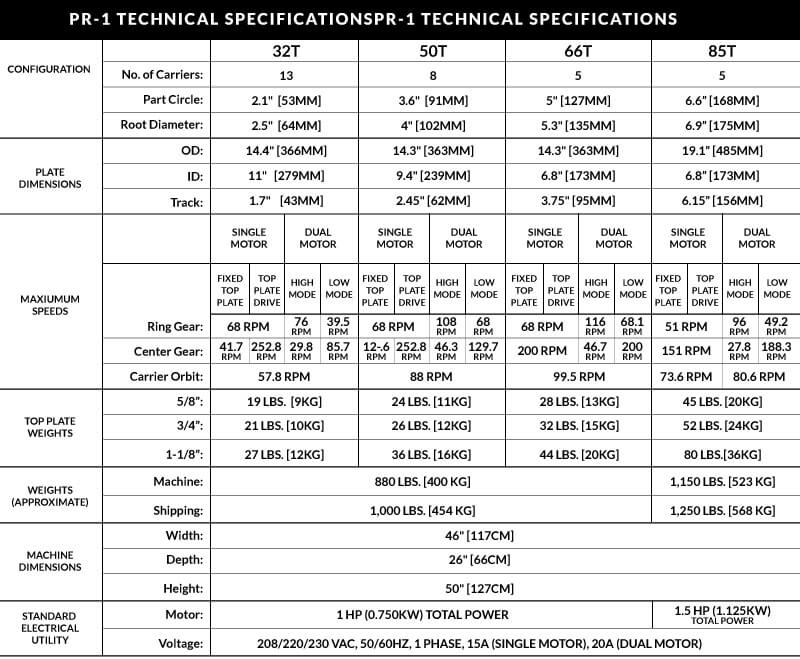
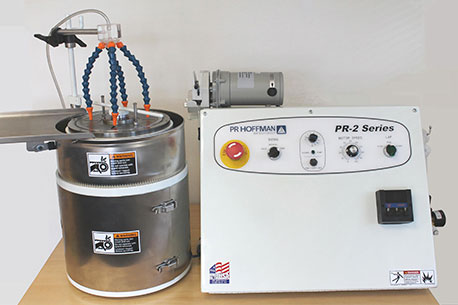
PR - 2
Equipment
- 32 tooth carrier configuration
- Smooth cast iron plates
- Stationary bottom plate
- Floating, non-rotating top plate
- Cast iron ring and center gears
- Driven by single variable speed motor
- Mechanical transmission drives the outer ring gear and center sun gear at fixed gear ratio
- Overrunning clutch provides soft stop at end of process cycle and allows operator to manually rotate ring and center gears
- Bottom plate height adjustment mechanism
- Post and hanger for storing top plate when machine is not running
Control console
- Illuminated start/stop selector switch, master speed control knob, manual or timer control selector switch, emergency stop pushbutton and main disconnect selector switch
- Digital process cycle timer control
Top plate manually raised and lowered onto parts being processed
One year warranty
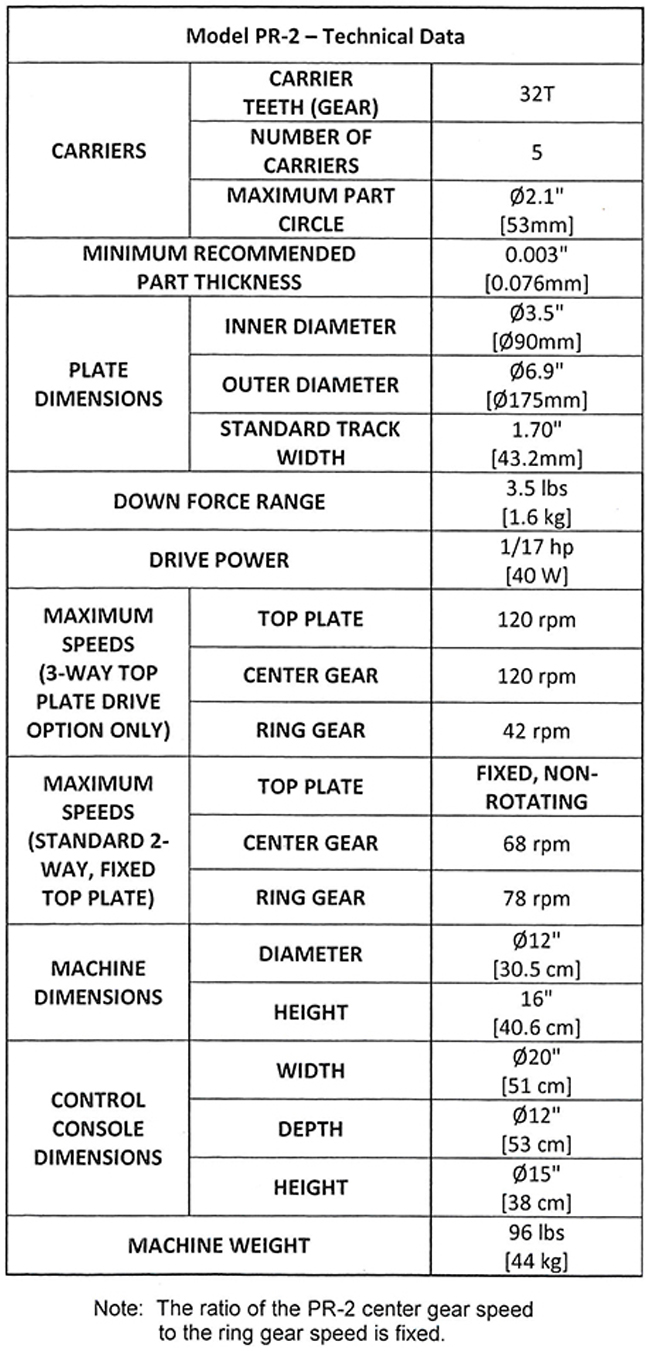
SERVO RS Series
In 1990, PR Hoffman introduced the Servo-RS Model 1500, the first machine in its new Servo RS™ series. The design of this machine series drew from over 50 years of experience with developing and building double-side planetary lapping and polishing machines. In the following years, we have expanded and refined the family of Servo RS Machines to include the model 1900, 3100, 5400, 6600, and 7600 double-side machines, which feature nine carrier work holder sizes that range from 2.5” (64mm) to 27.7”(703.6mm) in diameter. In addition we have our SSP-619 single-side polisher for work pieces up to 18”(450mm).
The base machine designs in the Servo RS™ series all employ a fixed bottom plate, independently programmable rotating top plate, center gear, and ring gear, and precise, servo-controlled down force control. We also offer a counter-rotating 4-way machine design option on the 1900 and 3100 models. All machine motions incorporate advanced drive technologies for precise control and high efficiency.
All PR Hoffman machines utilize a common motion controller and Windows PC-based software with touchscreen interface. They offer a range of optional features as well as design customization in order to address individual needs of customers.
Standard Features
- Smooth cast iron plates
- Fixed bottom plate
- Self-aligning swivel-mounted top plate
- Independently programmable top plate, ring gear, and center gear rotation using servo motor motion controls
- Stainless steel ring and center sprockets with spring pins
- Servo-controlled downforce with load cell feedback
- Retractable ring gear
- Thick-section plates and sub-plates for improved flatness and stability
Automatic slurry feed system
- Pump and mixer are remote controlled by process recipe
- Slurry tank and distribution lines, with recirculation available
- Variable speed propeller-style mixer with controls at mixer motor
- Variable speed, reversible peristaltic pump with controls at panel
Automatic flush water system and hand sprayer
- Flush water is controlled by process recipe
- Flush flow control valve and distribution lines
- Teflon hand-held sprayer
- All components are compatible with deionized water
On-site machine install, set-up, and training
One year warranty
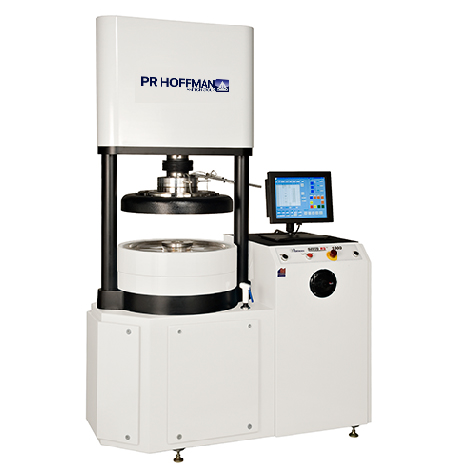
Servo RS 1900
Counter-rotating bottom plate 4-way configuration
Plates
- Serrated cast iron for lapping
- Stainless steel for polishing or fixed abrasive lapping
- Ductile Martensite iron fine-grain lapping plates for scratch-free lapping of parts with fine particle slurry
Stainless steel ring and center gears
Digital gauge
- Thickness control for lapping
- Crash protection for lapping and polishing
Water heated and cooled bottom plate temperature control system
Slurry system
- Recirculating slurry
- Multiple or high-capacity peristaltic feed heads and distribution lines
- Centrifuge system
- Slurry tank heating and cooling system
- Variety of customizable configurations available
Chemical injection system
- Auxiliary peristaltic pump and tank system
- Chemical injection pump controlled by process recipe
Wide variety of accessories available
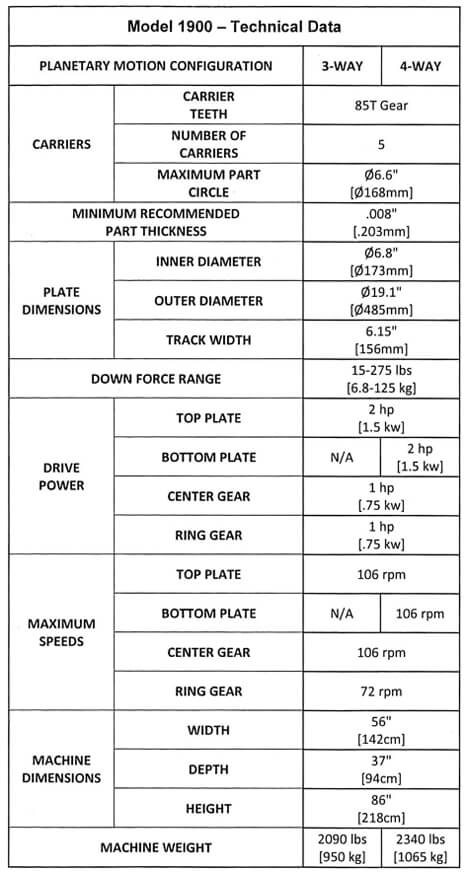
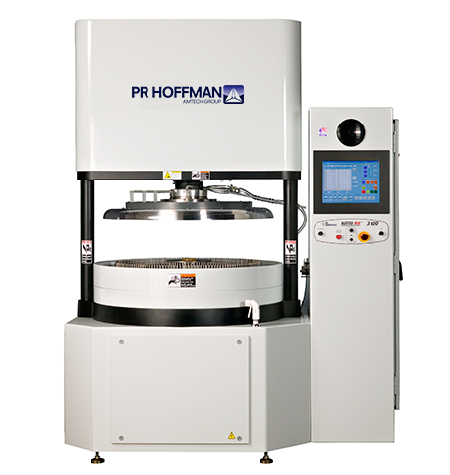
Servo RS 3100
Counter-rotating bottom plate 4-way configuration
Plates
- Serrated cast iron for lapping
- Stainless steel for polishing or fixed abrasive lapping
Stainless steel roller pins on ring and center sprockets
Digital gauge
- Thickness control for lapping
- Crash protection for lapping and polishing
Automatic Lapping Control (ALC)
Water heated and cooled bottom plate temperature control system
Slurry system
- Recirculating slurry
- Multiple or high-capacity peristaltic feed heads and distribution lines
- Centrifuge system
- Slurry tank heating and cooling system
- Variety of customizable configurations available
Chemical injection system
- Auxiliary peristaltic pump and tank system
- Chemical injection pump controlled by process recipe
Wide variety of accessories available
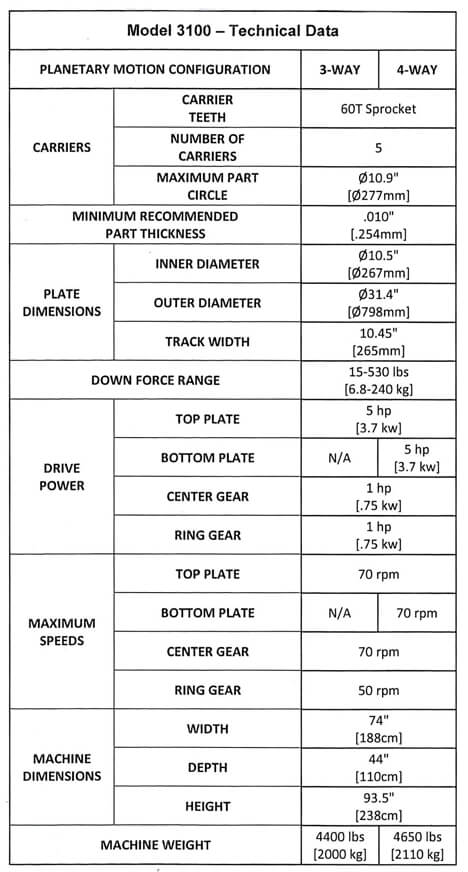
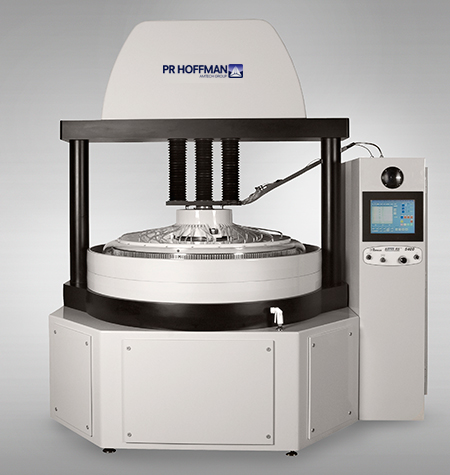
Servo RS 5400
Plates
- Serrated cast iron for lapping
- Stainless steel for polishing or fixed abrasives
- Cast iron with stainless steel cladding and slurry inserts for polishing or fixed abrasives
- Ductile Martensite for lapping with fine abrasive
Stainless steel ring and center sprockets
Digital gauge
- Thickness control for lapping
- Crash protection for lapping and polishing
Automatic Lapping Control (ALC)
Water heated and cooled plate temperature control system for both top and bottom plates
Slurry system
- Recirculating slurry
- Multiple or high-capacity peristaltic feed heads and distribution lines
- Centrifuge system
- Slurry tank heating and cooling system
- Variety of customizable configurations available
Chemical injection system
- Auxiliary peristaltic pump and tank system
- Chemical injection pump controlled by process recipe
Wide variety of accessories available
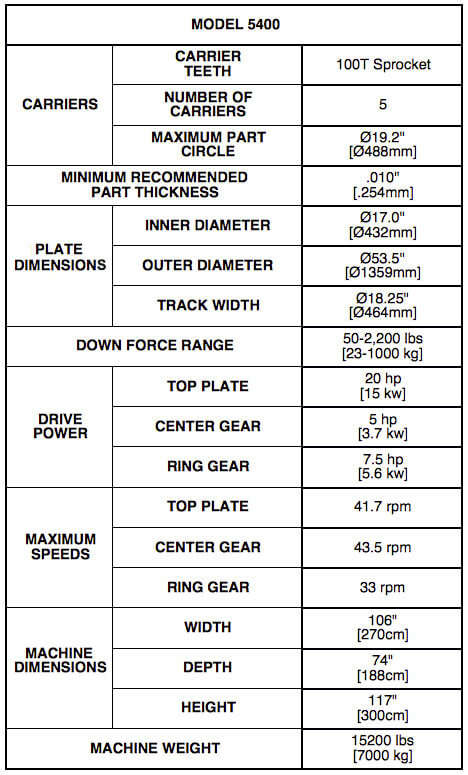
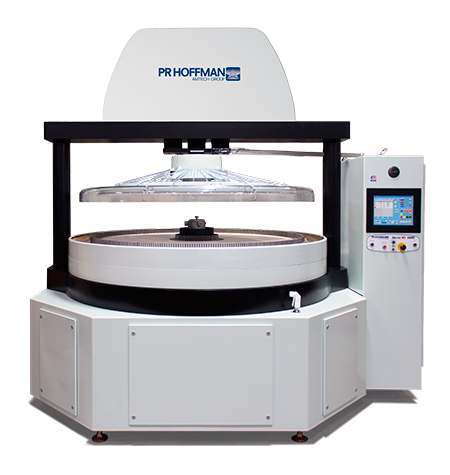
Servo RS 6600
Plates
- Serrated cast iron for lapping
- Stainless steel for polishing or fixed abrasives
- Cast iron with stainless steel cladding and slurry inserts for polishing or fixed abrasives
- Ductile Martensite for lapping with fine abrasive
Stainless steel roller pins on ring and center sprockets
Digital gauge
- Thickness control for lapping
- Crash protection for lapping and polishing
Automatic Lapping Control (ALC)
Water heated and cooled plate temperature control system for both top and bottom plates
Slurry system
- Recirculating slurry
- Multiple or high-capacity peristaltic feed heads and distribution lines
- Centrifuge system
- Slurry tank heating and cooling system
- Variety of customizable configurations available
Chemical injection system
- Auxiliary peristaltic pump and tank system
- Chemical injection pump controlled by process recipe
Wide variety of accessories available
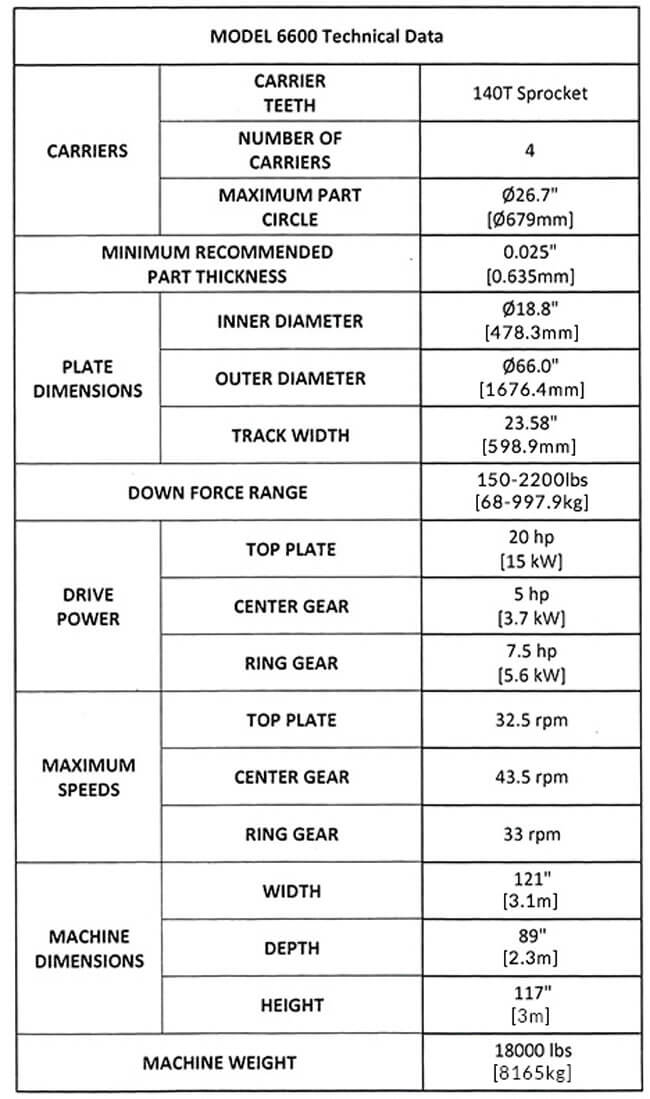
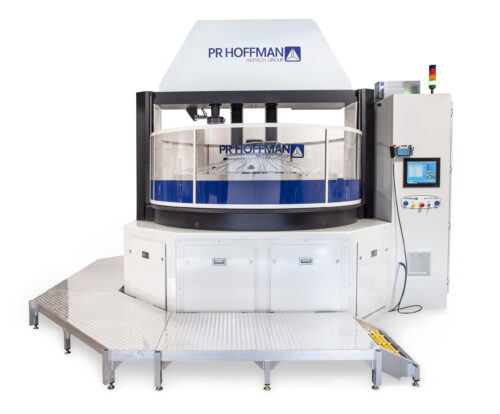
Servo RS 7600
The RS 7600 is a large production machine that can accommodate larger part sizes. This versatile machine can conduct a range of basic operations as well as multi-step and highly complex operations. The RS 7600 can support high removal rates on robust components, or it can be used for intricate/delicate components.
Machine Highlights:
- Operator-friendly features of legacy GUI
- Ease of operator use through single point load & unload
- Bottom plate and top plate rotation sync’d during unload for wafer tracking
- SECS/GEM compatible
- Enhanced safety and ease of cleaning with split enclosure
- Compatible with PRH DS Automation Cell
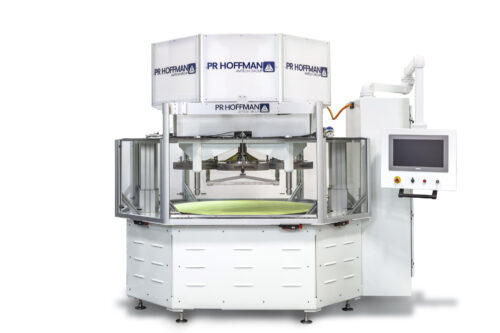
SSP-619
The SSP-619 is specifically designed to withstand a wide range of slurries at extreme pH levels and temperatures.
Exposed surfaces of the machine are chemically resistant to the interactions of slurries, thus improving machine cleanliness, reducing clean up time, and improving wafer quality. The SSP-619 offers innovative features and capabilities that maximize part load size and reduce dedicated operator time.
Machine Highlights
- Chemically resistant design and treated surfaces
- Independent polishing head rotation and pressure controls
- Ease of use for operators
- Convenient load/unload station
- Unique dovetail carrier design
- practical for manual mode
- critical for automation mode
- Temperature controlled processing
- Water cooled bottom platen
- SECS/GEM compliant
- Robotic cassette-to-cassette automation option available