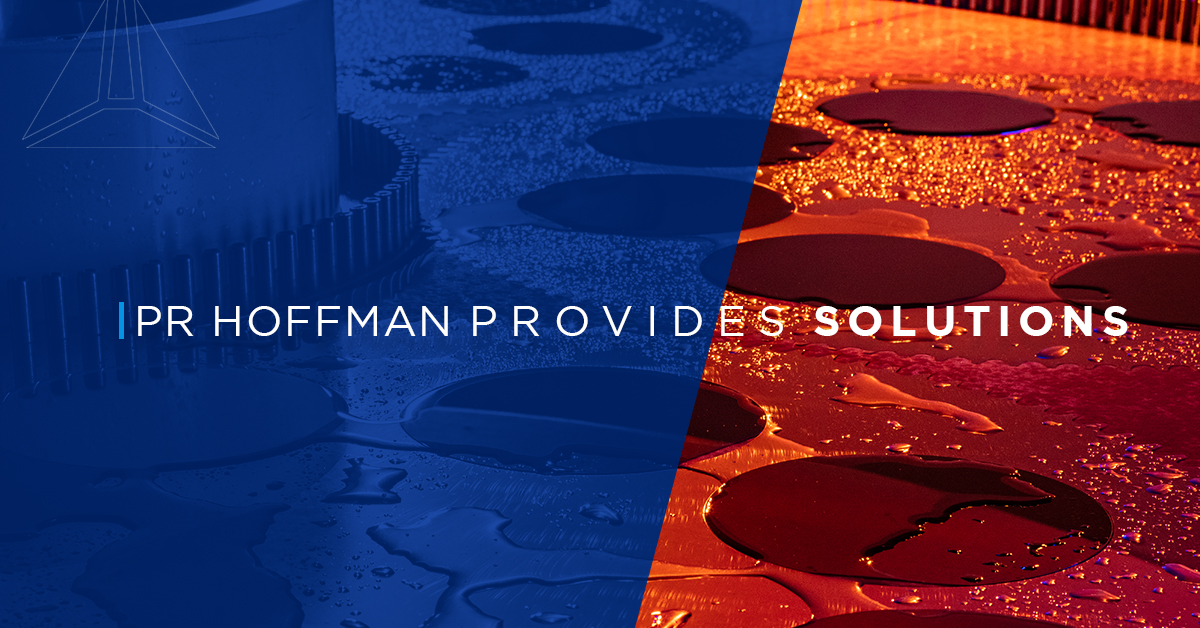
Are You Optimizing Supply Chain Disruptions?
Over the past 2 years, our world has changed. One of the biggest lessons we have learned is that adapting to adversity and making positive changes can keep our businesses fully operational.
The past 2 years have created significant turmoil for nearly every industry. Sourcing everything from raw materials to consumable goods has become a challenge at every stage of the supply chain. As businesses struggle with labor shortages and freight backlogs, manufacturers are feeling the pinch.
Certainly, the current supply chain conditions are challenging; the fragile ecosystem of global supply chain is a reality in manufacturing. As we all know, the network of our global supply chain is especially delicate for manufacturers. However, companies that innovate and adapt can actually use current conditions as a way to rise above their competition.
The following are recommended strategies to help you optimize supply chain disruptions:
Analyze your supply chain.
Assess the moving parts of your manufacturing and fulfillment processes. Know where all your consumables and materials originate, their cost, and their lead time for procurement, you can determine whether you need to fill any gaps or anticipate delays.
Consider placing larger purchase orders or paying more for expedited shipping.
Communicate with your customers and suppliers to set realistic expectations for deliveries or delays.
If you anticipate an item could take five months to arrive, for example, provide that time frame upfront. Promising delivery in 2 weeks, only to repeatedly delay, could create trust—and therefore loyalty—issues for the client in the future.
The biggest mistake a business can make is to let customers plan for product deliveries and then repeatedly be let down. Be up front with your customers to let them know you’re facing longer lead times and to set expectations that will allow them to plan accordingly.
Likewise, stay in regular contact with your own suppliers to remain aware of additional delays that may be mitigated with advanced knowledge.
Confirm pricing and delivery.
Volatility in the market is making costs of raw materials and fuel for shipping unpredictable. Be proactive and confirm pricing before making purchase orders to ensure there are no surprises. Aligned with good communication practices, confirming pricing keeps lines of communication open and helps to coordinate expectations between you, your suppliers, and your customers.
Use a system to root out orders that are not confirmed by your suppliers. A supplier may have an order but have no idea when it will be ready for shipment. You could be expecting it next week, but because it was never confirmed, you as the customer never realized it was not acknowledged.
Ensure you have sufficient safety stock inventoried.
Safety stock creates a proactive buffer against the potential for stockouts when delays in the supply chain create unexpected challenges for production. Depending on your product, experts suggest maintaining 10-20% of your stock ready to go; however, determining your specific safety stock needs will depend on the unique ecology of the supply chain that your products are part of. Review and adjust your system’s min/max values, and reorder quantities. In addition, update any outdated standard lead times.
Assess your inventory management systems.
Inventory management is critical. Ensure you have a thorough understanding of your current stock as well as the ways in which your management systems work to reflect numbers. A good inventory management system will allow you to automate processes and synchronize online and in-person sales. Additionally, including a waitlist option to your inventory management system will allow customers to recognize that while you might be currently experiencing a stockout, you plan to have the item or material available in the future.
We are in this together.
Over the past 2 years, our world has changed. One of the biggest lessons we have learned is that adapting to adversity and making positive changes can keep our businesses fully operational. We invite you to take some time and review your supply chain and proactively work with your supply partners. By thinking and acting outside of our comfort zones (or former standard operating procedures), we all can be proactive with our critical partners for the good of our customers.